Working with a luthier to build a custom guitar, Part II
(Brian Johnston | Posted 2011-07-18)
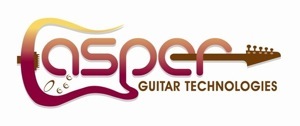
Editor's note: This is the second of a series by Brian Johnston about his experiences in working with a luthier to develop a custom guitar. Additional entries in the series will appear on MGR on Mondays.
Last week we first looked at how I came to develop the idea of having a custom guitar made for me by luthier Stephen Casper of Zero Impact Guitars, aka Casper Guitar Technologies.
The project shifted to a more concrete gear with a verbal update on July 2, 2011, when Stephen and I discussed several issues. The first aspect was to establish all the hardware to be used, including pickups and bridge type. He specializes in developing his own single-coil pickups, and he explained how these are crafted – hand-wound to maintain his quality of standards and to match the sounds forged in his imagination. For my guitar, however, he plans on using humbuckers. At this point I’m uncertain of the neck pickup, but the bridge pickup will be the DiMarzio Mojo as it produces the right tone relative to my taste and desired tone, but also Stephen’s musical background and understanding of what I am looking for.
A Schaller tremolo will be mounted in a routed slot, and this will provide a low profile to the picking area, similar to many Ibanez and Strat models. A top flat-mount bridge system was considered, but based on the guitar(s) I tend to select in my daily playing, that option did not win the day. As well, Stephen’s guitars have the reputation of holding tuning, even when the axe-wielder is a whammy kamikaze, and so I’m looking forward to testing those waters. The shape of the headstock also was confirmed and agreed upon, and although I had the opportunity to select or design any shape, I opted for the Zero Impact trademark design.
We also addressed the body’s finish once again, as how this looks in the end can make or break how someone envisions his or her custom guitar. Stephen explained how color especially can be an issue with many buyers who forward a chip or color sample, and then when he sends a photo back via email to show the end product of the painted body it does not always reflect, necessarily, the original sample. As most people know, and particularly those involved in the digital graphics field, every computer monitor has its slight nuances in regard to tint or hue reproduction insofar as true representation or accuracy is concerned, but when a sample is brought to a paint shop, rest assured it is a dead-on match or so close you cannot tell the difference. Consequently, there is some give and take when it comes to communicating via the Internet with photo images, but Stephen’s reputation made it obvious that he had no complaints with the end product and his customers’ satisfaction.
My guitar will not have a paint coating, however, but a clear matte finish to show the natural Swamp Ash grain. I have several painted guitars, but none that is ‘au natural.’ Stephen uses Behlen’s nitro cellulose spray lacquer, which he believes generates the best results, in a very hard and solid material once cured that will last a long time and age very well. However, the important thing about this coating is that the wood is allowed to age much better than the thick varnishes and enamels most companies use. In effect, wood takes on different sound characteristics via aging, which affects and improves an instrument’s timbre and tone qualities – which also can affect the emotive aspect of one’s playing.
Now, to give this project more life, Stephen forwarded me a photo of the neck materials, which arrived only days ago, including the blank maple neck that will be shaped via tools and hand, 6105 fret wire, truss-rod, and the rosewood fingerboard. This will be a bolt-on neck, and although some writhe at the thought of bolt-ons, it is because two-piece guitars typically do not have the sustain qualities of many neck-through-body designs. This has not been an issue for Stephen as the tightness and precision melding of the neck and body results in sustain that matches or rivals the best guitars available. The hand-crafted precision is far different than what can be expected in mass-production factories; and his attention to detail and precision fit is so extreme that he routes and fits the pickups and bridge only after the neck is attached to the body.
Seeing the neck in the ‘raw’ does make the experience more authentic, and around the 7th of July it becomes more a reality when he receives a grade-A piece of swamp ash to make the 1-piece body. Many inexpensive guitars (and even some more expensive models) will consist of multiple pieces of wood (whether side-by-side or layered), but this baby will be one solid piece.
My next consideration will be the type of selector switching I would like. Stephen has his own ideas, but I’ll be putting in my two cents to see which option is best, or if we come up with a hybrid solution.
Part III of the series will appear on MGR next Monday.
More about Casper Guitar Technologies
My #1 goal is to produce instruments that present little or no impact on the environment during the manufacturing process.
• I use materials that are tried and true to the art of lutherie.
• I use science and technology to help bring out every drop of tone from any given combination of materials.
Casper Guitar Technologies was established in 2007.
It has evolved from my longtime business of Casper Technologies where I performed modifications to guitars, modified parts and enhanced the tone for 100’s of local and regional guitar players since 1985.
I strive to achieve my shop goals by using sustainable growth and FSC Certified materials, solar powered LED lighting and 12V charging systems for hand-held tools and my computers, low VOC finishes and other methods that are proven to minimize ecological impact.
I am a self-trained luthier, descendent of French Cabinet Makers. Trained by my Grand Father in the fine art of cabinetry, I’ve been taught the patience and the techniques of hand shaping and assembly of fine wood.
“Guitars are my passion. I will continue to explore and learn the art until I can no longer"